Processus de fabrication du banc de tour
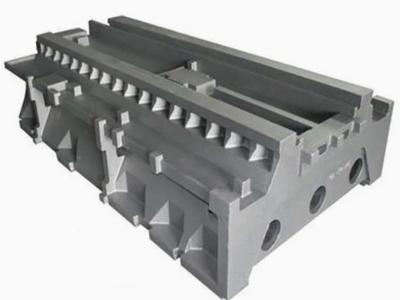
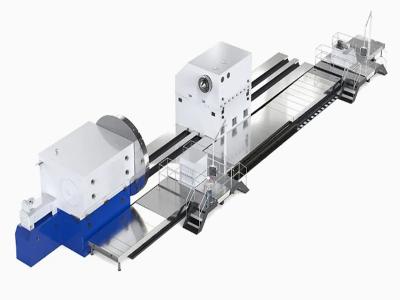
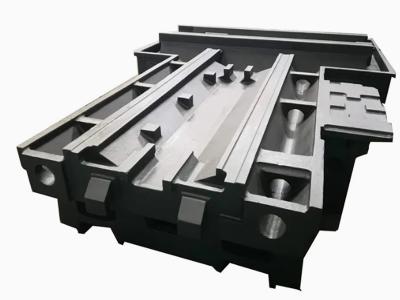
Nom du produit: | Processus de fabrication du banc de tour |
Mots-clés: | Processus de fabrication du banc de tour, processus de fonderie du banc de tour, ébauche du banc de tour, traitement de surface du banc de tour |
Industrie: | Mécanique et électrique - Industrie de fabrication de machines-outils, de machines et d'équipements |
Artisanat: | fonderie - autre |
Matériel: | Carbure |
Fabricants de transformation
- Il existe des fabricants de 59 qui proposent des produits similaires
- Il existe des fabricants de 149 qui fournissent cette technologie de traitement
- Il existe des fabricants 113 qui fournissent ce service de traitement de matériaux
- Il existe des fabricants 137 qui fournissent des services de traitement dans cette industrie
Détails du produit
Le processus de fabrication du banc de tour implique plusieurs étapes visant à garantir la précision, la résistance et la stabilité du banc, afin de répondre aux exigences dusinage de haute précision des tours. Voici les principaux processus de fabrication du banc de tour et les points clés des techniques, compilés à partir des informations disponibles :
1. Sélection des matériaux
- Matériaux courants : Les bancs de tour sont généralement fabriqués en fonte à haute résistance (comme HT250 ou HT300), en raison de leur bonne résistance aux vibrations, de leur rigidité et de leur résistance à lusure. Certaines machines-outils de haute précision peuvent utiliser de la fonte ductile ou une structure soudée en tôle dacier.
- Raison : La fonte possède dexcellentes propriétés de fonderie et une capacité damortissement des vibrations, ce qui la rend adaptée pour supporter les forces de coupe et les vibrations ; la structure en acier est utilisée pour lallègement ou les besoins de conception spéciaux.
2. Fonderie (ou soudure)
- Processus de fonderie :
- Conception du moule : Fabrication de moules en sable ou de moules métalliques de précision selon les plans de conception du banc, afin de garantir la précision des dimensions et de la forme de la pièce moulée.
- Fusion et coulée : Utilisation dun four à induction à moyenne fréquence pour faire fondre la fonte, contrôle de la composition chimique (comme la teneur en carbone et en silicium), et il est nécessaire de sassurer que la température est uniforme lors de la coulée pour éviter les défauts tels que les porosités et les retassures.
- Refroidissement et nettoyage : Après le refroidissement de la pièce moulée, un nettoyage par sablage ou grenaillage est effectué pour éliminer les grains de sable et la calamine de la surface.
- Processus de soudure (si une structure en acier est utilisée) :
- Utilisation de tôles dacier à haute résistance coupées et formées, et assemblage du cadre du banc par soudure.
- Un traitement de recuit est nécessaire pour éliminer les contraintes de soudure et assurer la stabilité structurelle.
3. Ébauche
- Objectif : Éliminer la surépaisseur de la surface de la pièce moulée ou soudée, et former la forme préliminaire.
- Équipement : Grande fraiseuse à portique, aléseuse ou centre dusinage CNC.
- Processus :
- Usinage de la surface de référence : Détermination de la surface de référence du banc (comme la surface inférieure ou la surface des glissières) pour assurer la précision du positionnement pour lusinage ultérieur.
- Fraisage : Ébauche des principales surfaces planes du banc (comme la surface de montage des glissières, la surface inférieure), en laissant une surépaisseur dusinage (généralement 2-5 mm).
- Perçage : Usinage des trous de montage, des rainures de liquide de refroidissement et dautres structures pour assurer la précision de la position des trous.
4. Traitement thermique
- Traitement de stabilisation :
- Stabilisation naturelle : Placer la pièce moulée pendant plusieurs mois à un an, en sappuyant sur lenvironnement naturel pour éliminer les contraintes internes, ce qui est peu coûteux mais prend beaucoup de temps.
- Stabilisation artificielle : Éliminer les contraintes résiduelles par stabilisation vibratoire ou stabilisation thermique (chauffage à 500-600 °C puis refroidissement lent), afin daméliorer la stabilité dimensionnelle.
- Objectif : Réduire la déformation lors de lusinage et de lutilisation ultérieurs, et assurer la stabilité à long terme du banc.
5. Usinage de précision
- Équipement : Fraiseuse à portique CNC de haute précision, rectifieuse ou rectifieuse de glissières.
- Processus :
- Usinage de la surface des glissières : La surface des glissières du banc de tour est une partie essentielle, qui nécessite une planéité et une finition de surface élevées (Ra0.8-1.6). Généralement, un fraisage de précision est suivi dune rectification, ou un usinage direct avec une rectifieuse de glissières.
- Contrôle de la planéité : Lerreur de planéité de la surface des glissières doit être contrôlée à moins de 0.01-0.02mm/m.
- Usinage de précision du système de trous : Alésage ou lamage des trous pour linstallation de la poupée fixe, de la contre-poupée, etc., afin dassurer la coaxialité et la précision de la position.
- Durcissement de la surface (facultatif) : Trempe à haute fréquence ou traitement de plastification (comme lapplication de bandes souples de glissières en PTFE) sur la surface des glissières, afin daméliorer la résistance à lusure et la résistance à ladhérence.
6. Traitement de surface
- Polissage ou pulvérisation : Polissage ou pulvérisation de peinture antirouille sur les surfaces non fonctionnelles pour améliorer lapparence et la résistance à la corrosion.
- Rainure de lubrification des glissières : Usinage de rainures dhuile de lubrification ou installation dun système de lubrification pour assurer un fonctionnement stable à long terme des glissières.
7. Inspection et étalonnage
- Équipement dinspection : Machine à mesurer tridimensionnelle, interféromètre laser, niveau, etc.
- Contenu de linspection :
- Précision géométrique : Vérification du parallélisme, de la planéité et de la rectitude de la surface des glissières.
- Précision de la position : Vérification des tolérances de position et de la coaxialité du système de trous.
- Qualité de la surface : Mesure de la rugosité et de la dureté de la surface.
- Étalonnage : Si des écarts sont détectés, un processus de grattage (manuel ou mécanique) est utilisé pour effectuer des corrections minimes sur la surface des glissières afin dassurer la précision.
8. Assemblage et mise au point
- Assemblage : Installation de la poupée fixe, de la contre-poupée, du chariot porte-outil et dautres composants sur le banc, et réglage de la précision dajustement de chaque composant.
- Mise au point : Exécution dun essai de fonctionnement pour vérifier les vibrations, le bruit et la précision dusinage du banc, et ajustement fin des glissières ou nouveau grattage si nécessaire.
Points clés des techniques
- Sélection des paramètres de coupe : Sélection raisonnable de la vitesse de coupe, de lavance et de la profondeur de passe en fonction du matériau et de la phase dusinage, afin déviter une usure excessive de loutil ou une déformation de la pièce.
- Contrôle de la précision : La précision dusinage de la surface des glissières affecte directement les performances dusinage du tour, et il est nécessaire de contrôler strictement la planéité et la rectitude.
- Élimination des contraintes : Le traitement thermique après la fonderie ou la soudure est une étape essentielle pour éviter la déformation lors dune utilisation à long terme.
- Sélection de léquipement : Les grands bancs nécessitent lutilisation de machines-outils CNC à grande course (comme les fraiseuses à portique) pour assurer lefficacité et la précision de lusinage.
Article précédent : Points clés pour linstallation des centralisateurs
Article suivant : Stabilisateur directionnel rotatif
Produits similaires
PlusAnalyse du processus dusinage des plaques dancrage fixes en acier au carbone
- Artisanat : usinage - Fraisage ou fraisage CNC
- Matériel : acier au carbone
Revêtement de cône mobile pour concasseur à cône
- Artisanat : -
- Matériel :
Fabrication sur mesure de poutres en H soudées S355JR pour la construction
- Artisanat : tôle - soudage
- Matériel : acier au carbone
Quels sont les procédés de fabrication utilisés pour les carters de ventilateurs axiaux
- Artisanat : tôle - soudage
- Matériel : acier au carbone
Stabilisateur de forage appliqué aux plateformes de forage pétrolier
- Artisanat : usinage - Usinage cinq axes
- Matériel : acier allié
Usinage combiné tournage-fraisage et contrôle non destructif de brides à paroi épaisse
- Artisanat : usinage - Tournage et fraisage
- Matériel : acier allié
Usinage de précision de profilés en U pour applications dans le bâtiment
- Artisanat : estampillage - Estampage ordinaire
- Matériel : Aluminium
Technologie de dénudage innovante : surmonter le goulot d'étranglement de la technologie de dissipation thermique haute densité
- Artisanat : Traitement de surface - autre
- Matériel : acier allié
Plus de produits
PlusAnalyse du processus dusinage des plaques dancrage fixes en acier au carbone
- Artisanat : usinage - Fraisage ou fraisage CNC
- Matériel : acier au carbone
Revêtement de cône mobile pour concasseur à cône
- Artisanat : -
- Matériel :
Fabrication sur mesure de poutres en H soudées S355JR pour la construction
- Artisanat : tôle - soudage
- Matériel : acier au carbone
Quels sont les procédés de fabrication utilisés pour les carters de ventilateurs axiaux
- Artisanat : tôle - soudage
- Matériel : acier au carbone
Stabilisateur de forage appliqué aux plateformes de forage pétrolier
- Artisanat : usinage - Usinage cinq axes
- Matériel : acier allié
Usinage combiné tournage-fraisage et contrôle non destructif de brides à paroi épaisse
- Artisanat : usinage - Tournage et fraisage
- Matériel : acier allié
Usinage de précision de profilés en U pour applications dans le bâtiment
- Artisanat : estampillage - Estampage ordinaire
- Matériel : Aluminium
Technologie de dénudage innovante : surmonter le goulot d'étranglement de la technologie de dissipation thermique haute densité
- Artisanat : Traitement de surface - autre
- Matériel : acier allié